核心应用场景与价值
1. 热处理过程追溯:
核心需求:淬火(通常伴随回火)是改变金属工件(如齿轮、轴承、轴、模具、刀具、军工部件等)机械性能(硬度、强度、韧性)的关键工序。精确控制工艺参数(温度、时间、冷却介质)对最终质量至关重要。
金属条码作用: 在工件进入热处理炉前,将耐高温金属条码标签 附着/标记在工件上。它能在整个高温加热、快速冷却(淬火)的严酷过程中幸存下来,并在处理后仍能被读取。
价值体现:实现从原材料到最终产品的全过程追溯。通过读取淬火后条码,可以:
精确追溯该工件经历的热处理炉次、工艺参数、操作人员、时间等信息。
确保工艺符合规范,进行质量控制(SPC)。
在后续检测或服役中出现问题时,快速定位原因(是材料问题、热处理问题还是其他环节问题)。
满足汽车、航空航天、医疗器械等行业的严格追溯法规要求。
2. 工序流转控制:
在大型热处理车间或多工序生产中,金属条码作为工件的唯一“身份证”,指导其在淬火、清洗、回火、检测等工序间的自动或半自动流转,减少错误,提高效率。
高温金属条码在淬火环境中的关键特性要求
1. 极端耐高温:
必须能承受淬火加热温度,通常在 **800°C 到 1200°C 甚至更高(如某些高速钢或特殊合金)。
材料本身在此温度下不能熔化、过度软化变形或发生有害相变。
常用基材:特种合金(如Inconel 600/625, Hastelloy X)或特定牌号的不锈钢(如310S/314)。普通不锈钢(如304/316)在此温度下强度会严重下降并剧烈氧化。
2. 抗热震/热冲击:
淬火的核心是急速冷却(从高温瞬间浸入水、油、盐浴或高压气体中)。
条码标签/标记必须能承受这种剧烈的温度骤变而不开裂、剥落或变形失效。
3. 抗氧化与耐腐蚀:
高温加热环境(尤其在空气或可控气氛中)要求材料具有极强的抗氧化(起皮)能力。
淬火介质(油、水溶性聚合物、盐浴等)可能具有腐蚀性,要求条码在冷却后及后续存储中耐介质腐蚀,防止信息模糊或标签损坏。
4. 机械强度与耐磨性:
在热处理前后,工件需要搬运、装夹,可能与其他工件或工装接触。
条码/标记需要具备足够的硬度和耐磨性,防止在流转过程中被刮伤、磨损导致无法读取。
5. 清晰可读性:
即使在经历高温氧化和淬火后,能被专用的耐高温/工业级读码器(通常是固定式DPM读码器或手持式激光扫描枪)稳定读取。
主要形式与安装方式
1. 金属条码标签:
材质:特种合金薄片(0.5mm -2mm厚)。
安装方式:
焊接:最常用、最可靠的方式。使用耐高温焊钉/焊点(通常与标签同材质或兼容)通过点焊、激光焊、电容储能焊等方式将标签牢固焊接在工件非关键受力面或预留区域。这是淬火环境下首选方式,能最大程度抵抗热冲击和机械冲击。
机械固定:在不能焊接或工件不允许焊接的情况下,使用耐高温金属扎带、夹具或耐高温胶(极少见,因为大多数胶在高温下会失效或碳化)固定。可靠性和抗冲击性通常不如焊接。
优点: 信息容量大,可包含序列号、批次号等丰富信息;可预制,安装相对快捷;可灵活选择位置。
缺点:增加额外零件(标签和焊钉);需要考虑焊接热影响区对工件局部性能的潜在影响(通常很小,但精密件需评估);成本相对较高。
2. 直接零件标记:
方式: 使用高功率激光打标机**直接在工件表面(非精加工面或预留区域)刻蚀出条码(通常是二维码Data Matrix或点阵码)。
优势: 无需额外标签和焊接,永久成为工件的一部分;消除了标签脱落风险;适用于空间受限或无法加标签的工件;长期成本可能更低。
挑战:
打标参数需精确控制,确保在经历淬火高温氧化后,标记对比度依然足够可读。有时需要在打标后做预处理(如涂层)保护标记区域,但增加了步骤。
对工件基材有一定要求(如可打标性)。
标记深度和热影响区需要控制,避免影响工件性能(特别是薄壁件或高应力区)。
在粗糙或曲面上打标和读取难度增加。
在淬火环境中的优势总结(相比其他标识方法)
永久性: 唯一能在整个淬火过程中存活并保持可读性的标识方案。
耐受性: 完美抵抗高温、热震、氧化、油污、水汽、磨损。
可靠性:提供稳定、准确的数据载体,支撑自动化数据采集和MES系统。
追溯性: 实现产品全生命周期,尤其是关键热处理工序的精确追溯。
合规性: 满足高要求行业的追溯和质量体系标准。
挑战与注意事项
成本: 特种合金标签材料和耐高温焊接工艺成本显著高于普通标签。
工艺集成 需要在热处理前工序(如机加工后、热处理前)完成标记和安装,需规划好生产流程。
位置选择:必须选择工件上温度相对较低、应力较小、不易被淬火介质强力冲刷、且便于后续读取的位置。避免精加工面、高应力区、配合面。
可读性验证:淬火后必须对条码可读性进行验证(100%或抽检),确保追溯链不断。
读码设备:需要配备适应车间环境(光线、油污、灰尘)的工业级读码器,对于DPM尤其需要专用的高分辨率读码器。
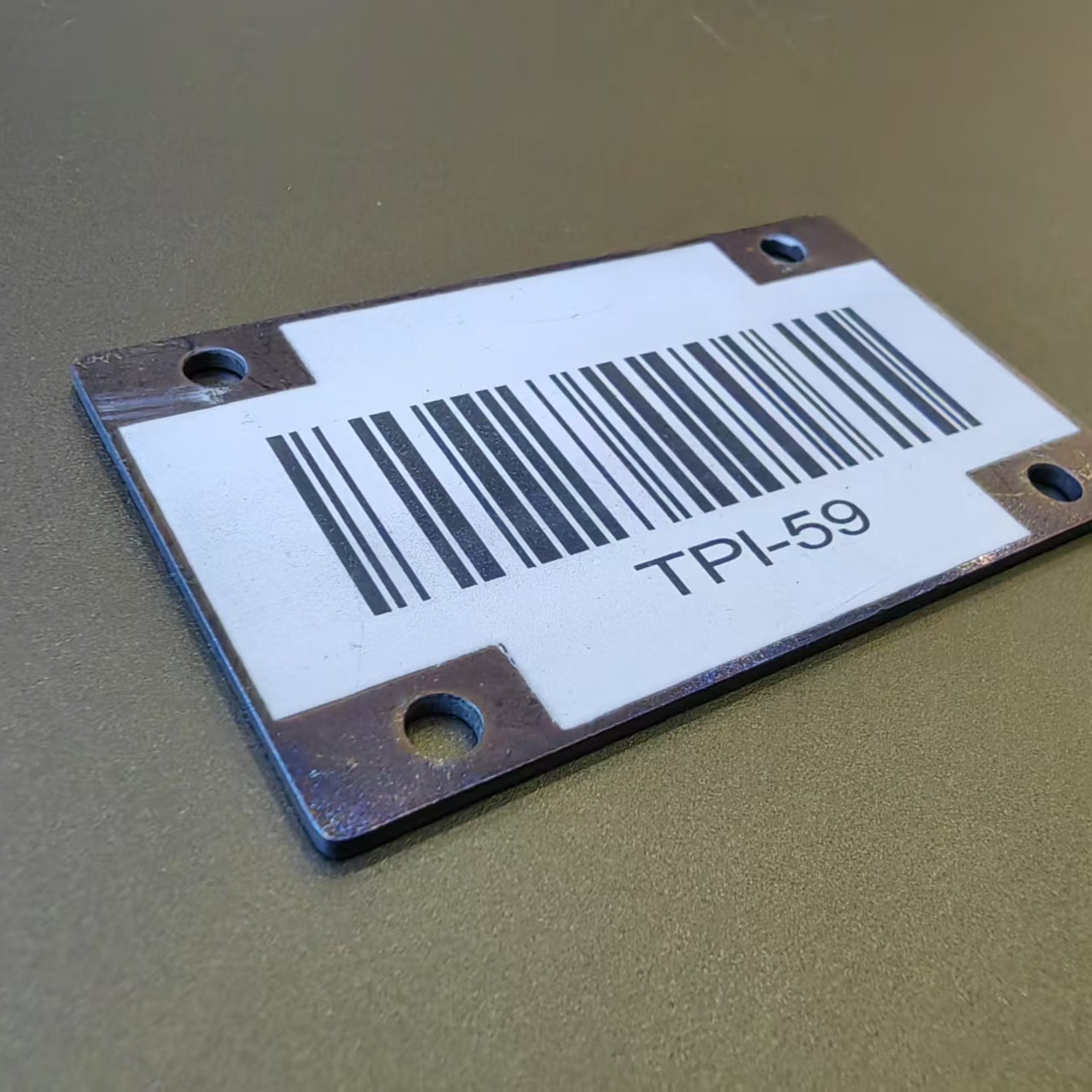